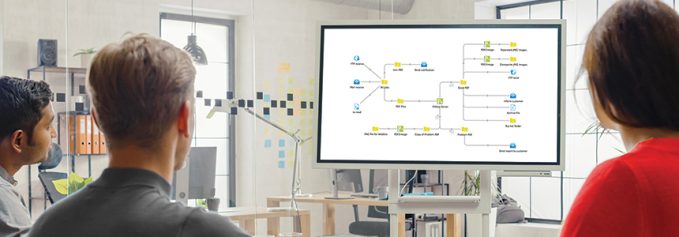
by Cassandra Balentine
The pace of technology advancements is rapid. Throw in a pandemic and all bets are off. Resistance to change is strong and consistent. However, modern challenges like a reduced labor pool make it more important for print providers to rethink their strategies. Automated workflows are one of the most effective ways to reduce labor and improve productivity.
Above: Significans Automation develops and integrates custom automated workflows.
“Many organizations still run things the same way they did ten years ago, but there does seem to be an increasing awareness and sense of urgency to improve and change,” admits Ryan Semanchik, president, Transformations, Inc.
Marc Raad, president, Significans Automation, suggests that modern, on demand printing is now feasible because of the speed, accuracy of stable technology, and above all—mature software. “Print service providers (PSPs) can confidently embrace a variety of possibilities due to investments in connected workflow processes and software with advanced customization.”
“Print businesses are familiar with the ongoing challenges they need to address—fewer resources, less skilled labor, more jobs, and faster turnaround. This makes it imperative to have tools that are easy to use, with less-skilled labor, in workflows that connect easily together. Those trends are driving the evolution of digital printing workflows today,” shares John Henze, VP of sales and marketing, EFI Fiery.
Steve Metcalf, chief IoT officer, Baldwin Technology, Amp, says a lot has been done to bring computer automation into the areas of web to print (W2P), prepress, color management, scheduling, MIS/ERP, or defect detection, but the integration and merging of “live data” that connect these processes was missing. “Most automation systems today operate in some form of a closed proprietary loop or in isolation of one another, leaving a cumbersome, manual process to merge information together for decision making and analytics. Overcoming this is the next step,” he notes.
Evolving Workflows
Workflow tools continue to evolve. Jonathan Malone-McGrew, CMP, G7 Pro, senior director, engagement, Solimar Systems, says the evolution in software and platforms focuses on rapid deployment, flexible deployment, remote working capabilities, tracking/reporting, reduced customization of the actual product or code, optimizations, integration points, and more flexible buying models.
“Print providers are demanding that software be cloud-based so it can be accessed anywhere, from the office or home,” agrees Therese McGady, marketing manager, Aleyant.
Adam Homsi, founder, InkCloud, also sees an evolution towards cloud-based and flexible rules management. “The realities of being a PSP means having to deal with many different facts and responding to them properly.”
“Software has developed at a much faster rate of speed over the past couple of years, which allows for easier integrations and greater visibility of the business analytics,” comments Graham Blanks, director of business operations, North America, DALIM Software.
As customer expectations increase, automated solutions needed to evolve to meet those demands. “Data management and the handling of files are two areas that have seen major changes in the past two years, with the biggest advancement involving APIs connecting to deliver postal processing to file composition to proofing without human intervention,” offers Semanchik.
Tomas Van Rossom, GM, Enfocus, believes the most significant evolvement of these tools is integration or the sharing of information between different types of software applications. “This is achieved with open REST API technology, which enables them to open their database with other applications. In some cases, these systems can also keep each other informed when information is added or changed. This charring can be initialized with data dumps or even better with web hooks where the updated information is instantly shared. The driving change is the customer. They are tired of having individual islands in their company that all have a level of information that is not shared.”
From an internal perspective, Amanda Newman, head of marketing, Tharstern, feels the pandemic highlighted the need for businesses to centralize their IT systems to ensure all employees could access the business data required to do their jobs and keep the company running.
“First, they had to make sure any employees working remotely could access the relevant software, and second that these disparate pieces of software were all hooked up together so essential business data was shared throughout the company,” explains Newman. “Because of this we saw an increase in the number of printers and converters who wanted to achieve this using their MIS solution—they realized that their MIS, because of its integration capabilities and the fact that it covers all the operational facets of a business, was ideally placed to act as the connectivity hub for a company’s technology stack. Whereas before the pandemic, we saw lots of companies focus on achieving this for their production and warehouse staff, the past two years we have worked on customer projects throughout the entire workflow, from sales and estimating right through to delivery and beyond.”
Print providers are increasingly forced to do more with less. “In the past two years, one of the largest problems with any producer of print, packaging, and other segments of the industry is the large number of employees aging out of the workforce. What happens when key people with the company’s knowledge base retire? This is driving a change towards automating systems and allowing younger employees to pick up skills that are practiced by their older coworkers,” explains
Jack J. Lafler, VP of sales and technology, HiFlow Solutions. “A modern MIS takes the brain trust of the company and systematizes it so that any worker, present or future, can access it,” he adds.
Today, printers and converters are able to achieve the ability to remove mundane operator tasks such as preflighting and allow for advanced preflighting and auto-fix capabilities with patterning and AI. “Integrated and optimized imposition, planning, nesting, step and repeat, and ganging is part of a workflow solution easily fulfilled with the least number of touch points in the business,” notes Raad.
The continued adoption of digital drives a lot of change relevant to production workflow and automation. “Digital printing has grown more capable and many customers have a digital plan to grow their business while scaling down their non-digital operations, especially as digital capability continues to evolve,” shares Levine.
Another change is a move from spot color inks. Instead of separating those spot colors to be printed, a fixed set of process inks can be used. “Today, digital presses are increasingly available with extra ink colors—red, orange, green, and violet. Those additional ink colors can help digital presses produce a wider array of spot colors without needing a specific special ink to match a special color. This is a practice that is also growing in the analog print world. In the past, some brands moved their print suppliers to extended color gamut (ECG) printing and seen tremendous efficiencies and savings. However, the complexities of the process and commercial purchasing practices somewhat limited the growth rate. With new tools and technologies, such as GMG OpenColor, GMG ColorServer, and GMG ColorPlugIn, installing an analog ECG workflow is more manageable and cost efficient for printers, creating more opportunities for supply chain partners to move the ECG,” shares Marc Levine, director of business development, GMG.
Bob Tilling, VP global sales, Kallik, sees more digitally based labels or artwork built in real-time using previously approved digital assets that the user knows are correct and appropriate.
Semanchik notices great strides in shipping automation, taking the previously manual steps of creating shipping labels and manual insertion to automated creation and machine inserting.
“Automated digital printing workflows, the type that can significantly reduce the time it takes for jobs to progress through preparation and onto a printer, have always been a key part of automation but continue to improve,” admits Henze. PSPs can really customize and create the correct automation workflow environment for their shops with the latest workflow tools.
Challenges and Bottlenecks
Workflow automation responds to bottlenecks throughout the production process. However, the journey to automation is also challenging for many.
Printers face major challenges on two fronts—the shortage of materials and the shortage of labor. “Increasing competition contributes even more strain. Automation is often the only way to keep the business alive in these conditions with increased efficiency, quality, and customer loyalty. However, investments in software integration are often superseded by other, more pressing challenges,” shares Alex Kozyavkin, director of marketing, Aurigma.
“Bottlenecks are caused by process, people, and machines. Without automation it is difficult to handle high volumes of short-run jobs and process them efficiently through print production to finishing to shipping. Automation helps to identify and eliminate job errors before running jobs, which increases the production speed as well reduce delivery lead time and waste. All of this adds up to better order fulfillment with maximum customer satisfaction,” says David Lunardi, VP of sales, OneVision.
Metcalf feels that in general, far too many hand-offs and manual steps still exist in print production workflows today, and it comes from the way systems and software have evolved. MIS/ERP grew from the need of transaction data processing, while presses and production equipment grew to automate the printing process on a single machine, and workflow was limited by closed, proprietary systems. A few standards have emerged such as JDF/JML, but to be fair, we haven’t had some of the tools and capabilities that we now can bring to bear. Big data and IoT are relatively new concepts that were out of reach for most companies until recently. We are now able to leverage the massive, low-cost computational speed and data storage available in the hyper-cloud—i.e. AWS, Google, Azure—to solve the next challenges in overcoming our bottlenecks to greater automation.”
Customer expectations along with manual tasks lead to bottlenecks today. “Everyone expects a more customized item, much faster. With manual work in the picture, this slows down the print production process and creates an opportunity for error,” shares Carissa Smith, marketing director, Tilia Labs.
“We’ve seen many providers struggle with automation because workflow has not been automated at intake. This makes it hard to make decisions further downstream,” offers Homsi.
Gemma Wood, product manager, Loftware, points out that many workflow challenges stem from three root causes—lack of accountability, visibility, and collaboration. “For example, artwork is often distributed to an average of six people before it can receive final approval and be integrated into the product labeling. That can’t happen until every single person—plus any third party—signs off the artwork. If people don’t know where they sit in that chain, it can create costly delays.”
Similarly, with manual artwork management processes, Wood believes there is limited visibility into who is supposed to do what and when, so project managers and leaders can’t easily see where the bottleneck is and resolve it. “An automated configurable solution designed specifically for product packaging can help companies overcome these challenges and transform their workflows to create a better process and speed time-to-market,” she adds.
The connectivity between W2P, MIS, and production workflow systems can determine the effectiveness of an automated workflow. “This not only speeds the communication of job data throughout the facility and allows workflows to adapt to each job. It also allows a printer to tie all business functions together—estimating, job setup, production, approvals, shipping, and billing,” offers Mike Agness, EVP, Americas, HYBRID Software.
Blanks agrees, noting the biggest bottleneck is the disconnect between different systems or communications between one another.
Production runs and accordingly print runs are getting shorter, says Danny Mertens, corporate communications manager, Xeikon. This means batch sizes can vary considerably but the incidence of short runs is becoming more frequent.
“High-speed digital printing presses typically don’t slow down when producing variable format content. Traditional finishing equipment, on the other hand, requires time-consuming manual changeover—thus creating a bottleneck,” explains Yashashree Potdar, workflow solutions analyst, Standard Finishing Systems. She points out that state-of-the-art finishing equipment features improvements in capabilities to improve production speed along with automation and software integration support that are helping to alleviate this issue.
“While we typically think of the printing process as containing the greatest number of variables for a service provider, finishing completes the job to profitability and timely delivery, and can easily be measured and monitored in real-time as to job status and productivity, as well as identifying bottlenecks, waste, and opportunities for improvement. All finishing equipment fundamentally generates live data, and for a data-driven organization, one can think of finishing as a natural extension to data aggregation to achieve a holistic ‘job flow’ picture to measure profitability,” comments Metcalf.
Addressing Automation
Modern print environments benefit from automation within their workflow tools. Solutions exist across the entire production lifecycle, but integration is imperative.
Read part one of this series, Tools that Drive Automation, online or in the July issue, part three is coming up in October. We also offer an archived webinar on the topic at dpsmagazine.com/webinars.
Read Part One, Tools that Drive Automation
Sep2022, DPS Magazine